Core Services
CAD Design
In our dedicated design suite, we combine innovation and precision to create bespoke packaging solutions that prioritise product protection, brand impact, and functionality. Using advanced CAD design software, we transform your requirements into detailed diagrams, and our state-of-the-art sample cutting machine produces prototypes in any required board strength. This enables you to test the fit of your product, trial the design on your assembly line, configure load quantities, check for strength, and ensure every aspect meets your exact needs – whether for secure transit, standout shelf appeal, or sustainable practices.
Printing
Brand enhancement and competitive edge
Our world class high-definition flexographic printing technology, combined with premium-quality papers, allows us to offer market leading quality – a capability unique to Ireland. As leaders in this field across the UK and Ireland, we collaborate with our customers to create market-leading printed packaging that drives their marketing and growth strategies.
Eco-friendly solutions
Our water-based printing process delivers exceptional quality without harmful plastics and solvents. All our packaging is fully recyclable, providing clients with an eco-friendly option to meet their sustainability goals. With increasing pressure on businesses to embrace environmentally conscious practices, packaging is the perfect starting point for impactful change.
World-class quality
We’ve made significant investments in cutting-edge technology and staff development to guarantee consistent, world-class product quality. Our advanced systems ensure precision and automatically remove defective items, while our dedicated team leverages extensive training to maintain the highest standards in every product we deliver.
Die-Cutting
Our factory is equipped with advanced die-cutting options: rotary and flat-bed. These state-of-the-art machines are designed to produce highly detailed die-cut boxes with unmatched accuracy. Known for their precision and reliability, our die cutters allow us to cater to the diverse and complex needs of our customers with ease.
Multi-Point Gluing
Our advanced multipoint gluers are expertly designed to fold and glue cardboard packaging with precision, ensuring a neat, ready-to-use box every time. From 4-point glued lids to pop-up crash-lock boxes, these machines offer exceptional versatility and efficiency. By maximising throughput, they allow us to meet your unique requirements with speed and reliability.
Stock Holding and Delivery
We ensure a seamless supply chain by maintaining optimal safety stock levels to prevent stockouts and reduce lead times. Through careful monitoring and forecasting, we provide a reliable buffer that minimizes disruptions and supports efficient operations.
Excellence in Packaging: Designed to Impress
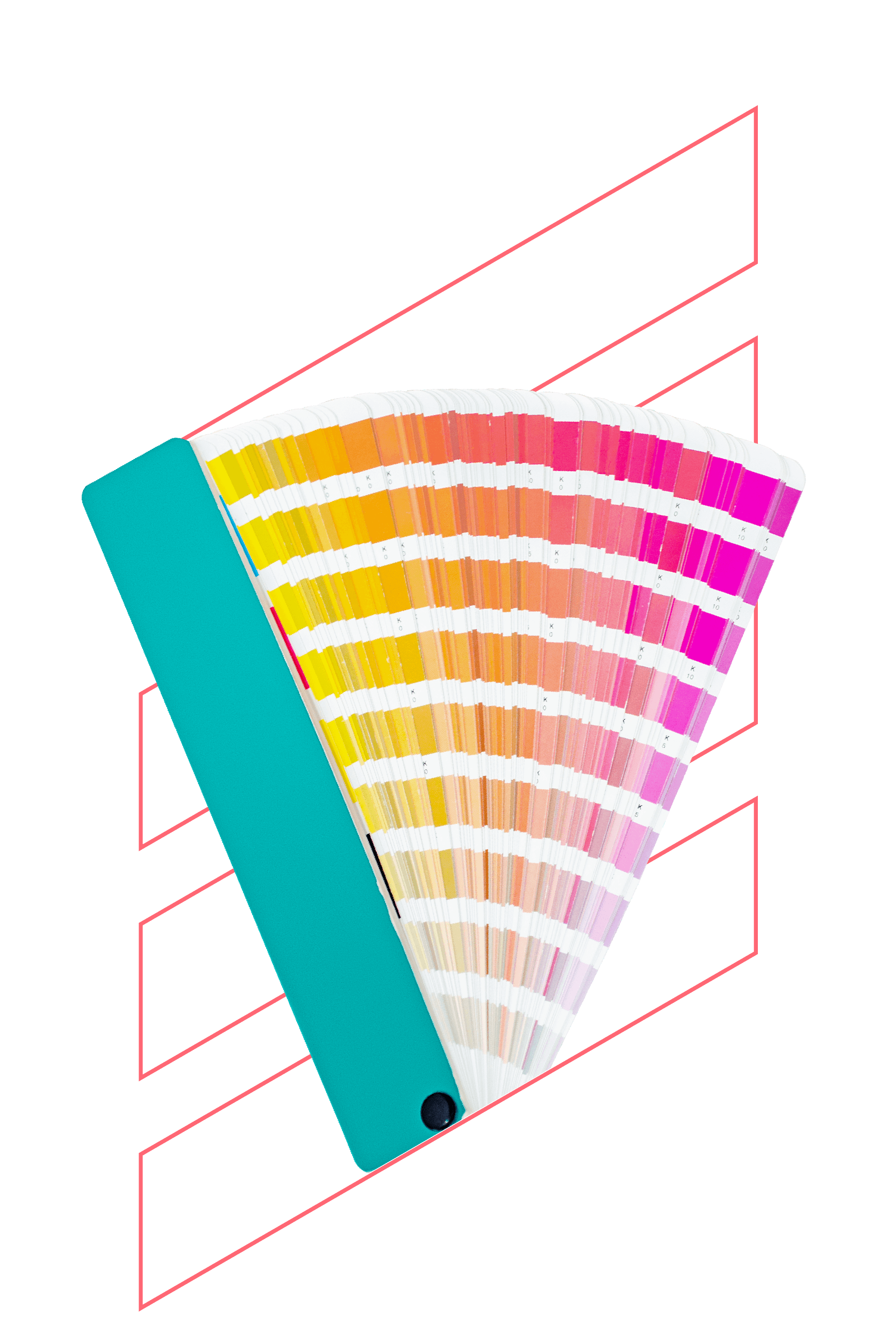
Innovation
More than 70 years in business serves as the platform for where we are today. From this strong footing, we grow through investment in technology and strengthening relationships with our clients and stakeholders. What we do on a daily basis for our clients prepares them to respond to market pressure and how we act as an organisation is no different.
Some challenges are constant, like ever shortening production runs or reducing waste but when it comes to responding to changing market conditions, we’re among the first to adapt.
Our end-to-end approach to corrugated packaging ensures that we can respond to changes in regulations quickly, keep up with the latest market trends or satisfy consumer demands in smarter, more flexible ways.
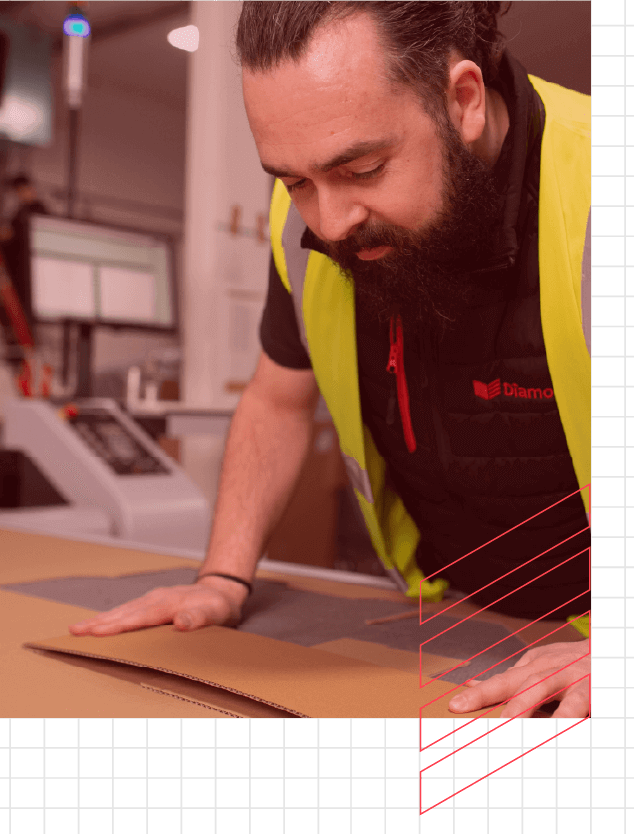
From order to delivery
Step 1
Initial Contact and Understanding Client Needs
From the outset, having a good understanding of the clients’ packaging needs and their challenges is essential to whatever solution we create. We listen, we establish how we can work in partnership, and then we figure out how we can help with their operations and even make improvements. The initial assessment discussions will cover everything from design and sustainability to scheduling and logistics considerations.
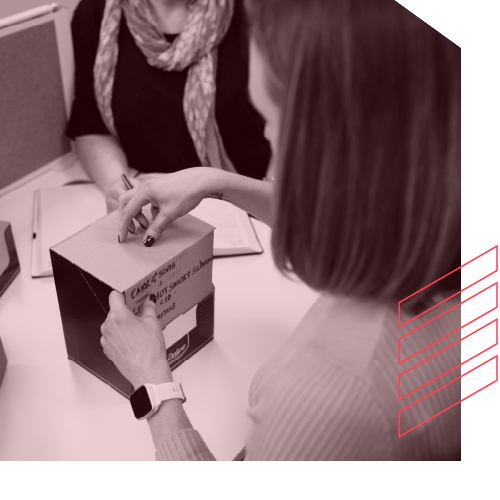
Step 2
Design Consultation and Concept Development
This is where we get the designers and engineers involved to come up with the best response to the client’s specifications. We take all factors into account, from weight and structure of the contents to transit conditions before the trial phase. Once this has been agreed, we prepare detailed quotations covering all costs before seeking client approval signalling the go-ahead for production.
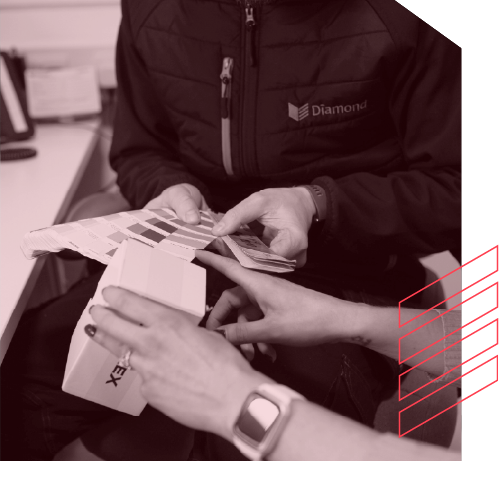
Step 3
Production, Quality, Delivery and Fulfilment
Depending on the complexity of the production, we break down each element in-house allowing us to be totally in control of the quality at each stage. Not only does this ensure the packaging is produced to mutually agreed standards, it reduces the lead times normally associated with outsourcing. Our storage solutions and Just-In-Time delivery services mean our clients always have exactly the amount of packaging they need according to their schedule.
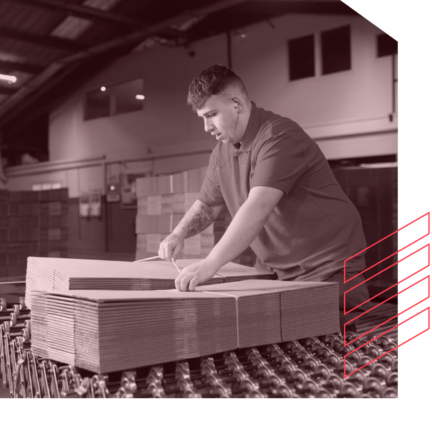
Step 4
Customer Care and Maintaining the Relationship
We believe the integrity of our products and our service speak to our commitment towards customer relationships. We work closely with our clients to make sure any printing, transit or functional issues can be resolved without delay and we welcome feedback as a means of ensuring continuous improvement. We aim to build the type of trust with each new client that can lead to new projects, improved ways of working together and mutual, sustainable business growth.
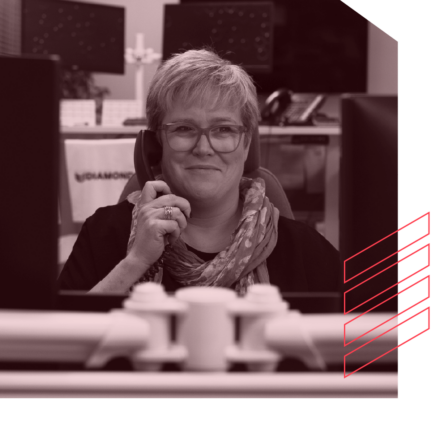
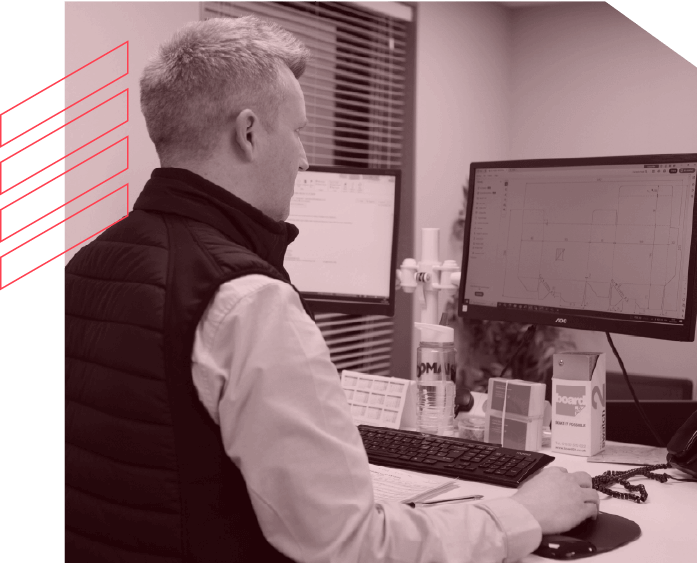
Work With Diamond
Here to help
Whatever your challenge, we can help you to achieve the outcome your brand deserves. Contact us today to find out what we can do for you.
Get in Touch